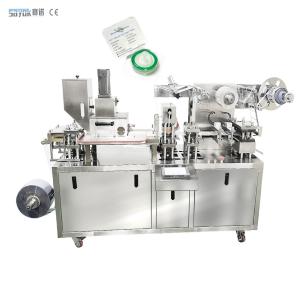
Add to Cart
As technology advances, blister packing machines continue to evolve with features such as intelligent control systems, remote monitoring capabilities, and data analytics for performance optimization. These advancements aim to improve efficiency, reliability, and product safety in blister packaging operations.
Packing Machine parameters | |||||||||||||||||||||||||||||||||||
|
Maintenance and Support: Proper maintenance is crucial for the efficient and reliable operation of blister packing machines. Manufacturers typically provide maintenance guidelines, training, and support for spare parts availability, troubleshooting, and technical assistance.
Blister Types: Blister packing machines can accommodate different types of blister packs, including standard blisters, deep-draw blisters, clamshell blisters, and wallet-style blisters. The choice of blister type depends on the product being packaged, its size, shape, and specific packaging requirements.
Material Compatibility: Blister packing machines can work with various materials, including PVC (Polyvinyl chloride), PVDC (Polyvinylidene chloride), PET (Polyethylene terephthalate), Aclar (Chlorotrifluoroethylene), and others. The compatibility of the machine with different materials depends on factors such as heat sealing capabilities, forming properties, and the product's sensitivity to moisture, light, or oxygen.
Machine Details:
1. Stainless steel quality, good in appearance and machine is more durable | |
2.The cylinder sealing method is used, with uniform pressure and clear texture, resulting in a flat and natural appearance. The sealing mold automatically separates when the machine stops, preventing scalding of the packaging material. | ![]() |
3. Heat Sealing System | ![]() |
4.Waste Material Winder
| ![]() |
5. Supports Multiple Packaging StylesExclusive molds can be customized according to customer needs.For more details, please consult customer service online. | ![]() |
6. Application | ![]() |